Six Sigma and Change Management for Sustainable Success
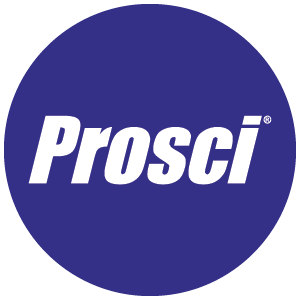
8 Mins
Updated: February 17, 2025
Published: October 1, 2024
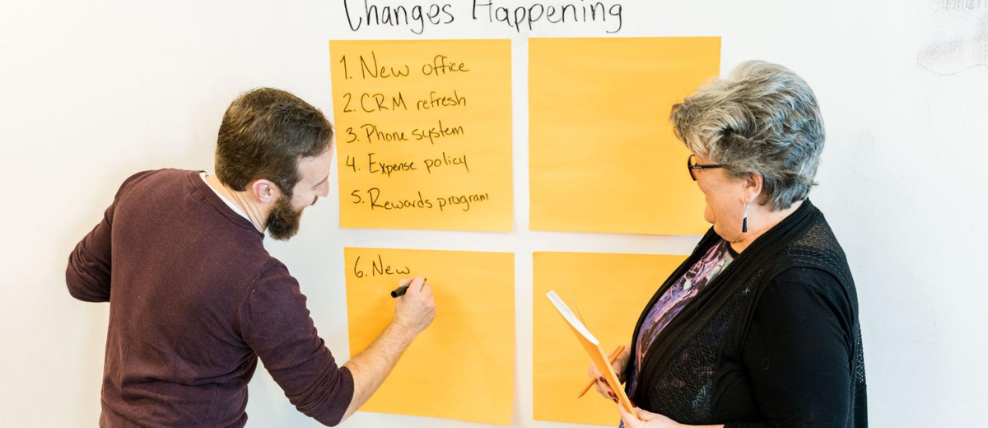
Organizations are constantly seeking ways to enhance their processes, increase their level of quality, and maintain a competitive edge. One effective approach to doing that is by implementing Six Sigma.
Developed in the 1980s, Six Sigma focuses on process improvement, enabling organizations to identify and minimize errors that impede performance, ultimately boosting efficiency. This approach can help achieve key objectives such as increasing customer satisfaction, reducing costs, and enhancing profitability.
However, to maximize the success and responsiveness of Six Sigma initiatives, it's beneficial to integrate it with a structured change management approach centered on the people side of change. When applied to Six Sigma projects, change management models like the Prosci ADKAR® Model and the Prosci Change Triangle (PCT) can help organizations achieve their goals.
In this article, we will explore how change management complements Six Sigma, enhancing its effectiveness and driving sustainable success.
What are Six Sigma and Lean Six Sigma?
Six Sigma is a data-driven, customer-focused approach to improving existing processes by identifying and reducing waste and defects to enhance efficiency. It utilizes quality management tools and techniques to achieve measurable and quantifiable financial returns, often structured around a data-driven improvement cycle known as DMAIC (Define, Measure, Analyze, Improve, Control) phases.
Originally developed by Motorola in the 1980s, Six Sigma has been used throughout various industries such as manufacturing, healthcare, financial services, and education to improve quality. Six Sigma seeks to reduce variation, leading to increased customer satisfaction and reduced operational costs. You can get certified in Six Sigma at different levels, including white belts, yellow belts, and green belts, all the way to master black belts.
Lean Six Sigma is a methodology that combines Lean key principles and Six Sigma practices. Lean focuses on waste reduction, and Six Sigma emphasizes reducing variation and the defect rate using data-driven approaches to improve overall quality and efficiency.
Lean is the first step in Lean Six Sigma. It's about removing waste. After that, Six Sigma reduces variation. Lean goes hand in hand with Six Sigma—they're practiced together in a single approach leading to Lean Six Sigma.
Let’s take a deeper look.
The Lean Six Sigma Methodology
Lean Six Sigma uses a modified structured approach known as DMAIC to improve processes, which consists of 5 phases.
The core methodology: DMAIC
Lean Six Sigma is an integrated approach that combines the principles of Lean and Six Sigma to enhance process improvement and efficiency. This methodology modifies the traditional Six Sigma framework by incorporating Lean's focus on waste reduction and process flow optimization. The core Lean Six Sigma methodology follows the DMAIC phases, which are tailored to exploit the strengths of both approaches:
Define
- Lean – Uses value stream mapping to identify waste and focus areas for improvement.
- Six Sigma – Defines project goals and customer requirements.
Measure
- Lean – Implements time studies and process flow analysis to understand current performance.
- Six Sigma – Collects data to establish baselines and measure performance.
Analyze
- Lean – Performs root cause analysis to identify sources of waste and inefficiencies.
- Six Sigma – Uses statistical analysis to identify causes of variation and defects.
Improve
- Lean – Applies Lean tools like 5S and Kaizen to streamline processes and eliminate waste.
- Six Sigma – Implements solutions to reduce variation and improve quality.
Control
- Lean – Establishes standard work and continuous improvement practices to sustain gains.
- Six Sigma – Uses control charts and other tools to monitor process stability and performance.
By integrating Lean’s focus on eliminating waste with Six Sigma’s emphasis on reducing variation and defects, Lean Six Sigma provides a comprehensive framework for achieving high-quality, cost-efficient and agile change. This modified version of Six Sigma enhances the methodology by ensuring that improvements are both statistically sound and operationally efficient.
Six Sigma Certification Programs
There are several Six Sigma certification programs available that aim to equip individuals with the skills and knowledge needed to effectively apply Six Sigma methodologies. These programs typically offer different levels of certification, from white belts to black belts, based on increasing levels of expertise and responsibility, which are:
- White Belt
- Yellow Belt
- Green Belt
- Black Belt
- Master Black Belt
For example, the Green Belt certification enables you to lead or support projects. Through these certifications, you can learn to apply Six Sigma to eliminate defects, meet customer requirements, and enhance quality in whichever industry you’re part of.
However, to achieve maximum efficiency in projects, the people side of change needs to be addressed via change management. Here's how you can do that.
Understanding the People Side of Change in Lean Six Sigma
If you’re in the middle of a Lean Six Sigma project and experiencing employee resistance behaviors or a lack of management support, you’re not alone.
Although implementing Lean Six Sigma tools and processes, including DMAIC, can provide direction for change, combining it with change management increases your organization’s chances of success. Prosci research shows that projects with effective change management are seven times more likely to succeed and are more likely to finish on time and within budget.
Benefits of Change Management
While Lean Six Sigma addresses processes, change management focuses on individuals. Why is this important?
Because managing the people side of change is a critical task of its own. Compared to data sets and statistical methods, people are more complex to manage due to the emotional dimensions inherent in human behavior. This is summarized well by Val Larson and Mike Carnell (of Six Sigma Applications) in their article, Developing Black Belt Change Agents:
“Why, then, if the change agent role is such an important part of the Black Belt identity, do we spend 4 to 6 months training the Black Belt candidates with maybe just a few hours of training on the process of change?” he says.
Carnell adds, “Perhaps it is a two-fold issue. First, change has undeniably been labeled as difficult. Second, dealing with change is ambiguous, even on a good day. The fact is, however, that the root cause of the difficulty is the same root cause of the ambiguity. The real issue is people! They aren't like a nicely defined data set where we can hit a few keystrokes, stack them, run an analysis, and, if it doesn't work out, delete that worksheet as if it never happened... People are much more complex than a data set."
Exactly. Managing the people side of change and securing management support are common challenges many organizations face during change initiatives, and change leaders are well aware of this:
"Without the support of senior leaders, change initiatives are destined to fail."
—Jack Finney, President and CEO, Six Sigma Academy
What does that mean for Six Sigma professionals? It means a Green Belt or Black Belt certification is not the end of the road in terms of certification and learning. It's simply your ticket to begin the change journey.
Change Management in Lean Six Sigma Projects
Certainly, the people side of change will challenge even the best Black Belt on your team, and the ambiguity of managing change may test their patience. Developing change management skills will reduce the personal stress associated with leading change projects, and investing in Lean Six Sigma produces greater returns.
Ultimately, your goal is to deploy your Lean Six Sigma projects effectively. Change management will be the most important companion discipline for realizing this goal.
By incorporating change management, Lean Six Sigma improvements become sustainable, ensuring that process enhancements are implemented and maintained over time. Change management facilitates a cultural shift within the organization, creating an environment that values continuous improvement. This cultural alignment is excellent for sustaining the benefits of Lean Six Sigma projects.
Applying change management strategies, such as those in the Prosci Methodology, can significantly enhance Lean Six Sigma projects. These strategies allow organizations to identify potential risks early and adapt strategies accordingly.
Our ADKAR Model is instrumental in this process. It focuses on the individual change journey, highlighting five key elements a person needs to change successfully: Awareness, Desire, Knowledge, Ability and Reinforcement. Achieving these milestones ensures that each person affected by the change is prepared and supported, which is crucial for the success of Lean Six Sigma projects.
From a single project to an enterprise-level initiative, the ADKAR Model can greatly increase visibility and responsiveness in Lean Six Sigma projects and programs. Lean Six Sigma, implemented at a site or enterprise level, represents a large organizational cultural change. Implementing a series of tools alone almost guarantees failure. A robust change management strategy, grounded in the ADKAR Model, greatly increases the success of a Lean Six Sigma program.
The Lean Six Sigma Define, Measure, Analyze, Improve, and Control (DMAIC) phases link closely with the Prosci ADKAR Model, a key component of our change management methodology and tools:
Prosci ADKAR Model in Project Phases
This shows that to achieve success, Lean Six Sigma and change management work hand in hand.
Change management should be integrated into the project lifecycle early on to achieve the success and sustainability of Lean Six Sigma initiatives. This involves engaging stakeholders from the outset, aligning project goals with organizational objectives, and continuously monitoring progress to ensure that both people and processes are prepared for the change.
By doing so, organizations can maximize the impact of their Lean Six Sigma projects and achieve lasting improvements.
Now let’s have a look at some real-world applications where implementing Lean Six Sigma led to successful outcomes.
Practical Applications and Examples of Lean Six Sigma
Lean Six Sigma has been successfully applied across various service industries to drive efficiency. Here are some examples.
Lean Six Sigma in healthcare: surgery
Challenges
A systematic review was conducted to analyze the effect of Lean Six Sigma on surgery at the NHS. Healthcare facilities, particularly surgical departments, faced significant operational inefficiencies, including delayed operating room start times, long patient waiting periods, and high turnover times between surgeries. Additional challenges included high complication rates, hospital-acquired infections, inadequate antibiotic prophylaxis, and rising operational costs despite resource constraints.
Lean Six Sigma interventions
The implementation of Lean Six Sigma methodologies focused on systematic process improvements using the DMAIC framework. Interventions included standardizing surgical techniques, optimizing workflow processes, creating one-stop pre-operative clinics, improving patient preparation protocols, enhancing team communication, and establishing clear staff roles and responsibilities across the department.
Outcomes
The results showed significant improvements across operating room efficiency and patient safety, reduced infection rates (MRSA down 60%), better antibiotic compliance (increasing to 86%), and decreased surgical complications.
Lean Six Sigma in manufacturing: repair process for military vehicles
Challenges
The manufacturing industry suffers from inefficient repair processes for MRAPs, with vehicles often parked haphazardly and worked on without a clear triage system.
Lean Six Sigma interventions
Through Lean Six Sigma, a triage system to assess incoming vehicles in the U.S. Army was implemented. Vehicles were categorized by repair needs (short-term, medium-term, and long-term). The overall workflow became more streamlined as vehicles moved through a standardized repair process similar to an assembly line, ensuring efficient use of resources and minimizing waiting times for different repair stages.
Outcomes
A dramatic increase in repair output in the current process—from fixing two vehicles to up to 20 vehicles per month—led to more effective use of repair resources and reduced downtime for important equipment.
Lean Six Sigma in pharmaceutical solutions: enhancing project success
Challenges
The pharmaceutical industry faces unique challenges when implementing Lean Six Sigma initiatives. Managing multiple projects simultaneously can be overwhelming, particularly when the human side of change—such as employee understanding, engagement and resistance behaviors—is not adequately addressed. A lack of clarity on how these projects align with organizational goals often creates additional barriers to success.
Ric McCormick, an experienced Lean Six Sigma Black Belt in the pharmaceutical sector, noted:
"While overseeing multiple projects, I realized that simply understanding the deliverables for each phase wasn't enough to manage a complex portfolio effectively. The lack of visibility into how these projects interacted with the organization's overall goals created challenges in maintaining focus and achieving desired outcomes."
Lean Six Sigma interventions
To address these challenges, organizations are increasingly incorporating structured change management approaches into their Lean Six Sigma frameworks. McCormick found that tools like the Prosci Change Triangle (PCT) Model were invaluable in integrating the technical aspects of Lean Six Sigma with the human elements of organizational change. This combination provided a more holistic approach to project execution, ensuring that both processes and people were aligned for success.
Outcomes
The integration of Lean Six Sigma with change management strategies yields measurable benefits for pharmaceutical operations:
- Increased employee engagement – Teams become more invested in project success when their concerns and contributions are actively addressed.
- Improved team cohesion – Cross-functional collaboration strengthens, reducing silos and enhancing problem-solving.
- Reduced resistance to change – Proactive engagement with employees fosters a culture of adaptability, paving the way for smoother project implementation.
- Sustained improvements – Aligning technical enhancements with organizational change ensures long-term success and continuous improvement.
These outcomes demonstrate that the true potential of Lean Six Sigma is unlocked when technical methodologies are complemented by strategies that prioritize the people side of change.
Why Lean Six Sigma Needs Change Management
Lean Six Sigma is a powerful methodology for reducing process variation and improving quality, particularly in highly regulated industries like pharmaceuticals. However, its success depends not only on technical execution but also on how well organizations manage the people side of change.
Effective change management complements Lean Six Sigma by addressing the human factors that influence project success, ensuring that improvements are adopted, understood, and sustained over time. By integrating change management principles into Lean Six Sigma projects, pharmaceutical companies and organizations of all kinds can enhance productivity, achieve higher-quality outcomes, and foster a culture of continuous improvement.