Process Improvement Methodologies and Change Management
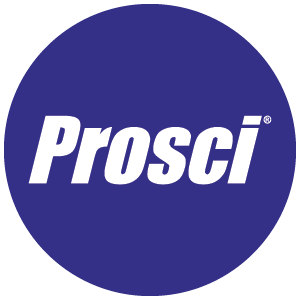
8 Mins
Updated: February 19, 2025
Published: December 1, 2024
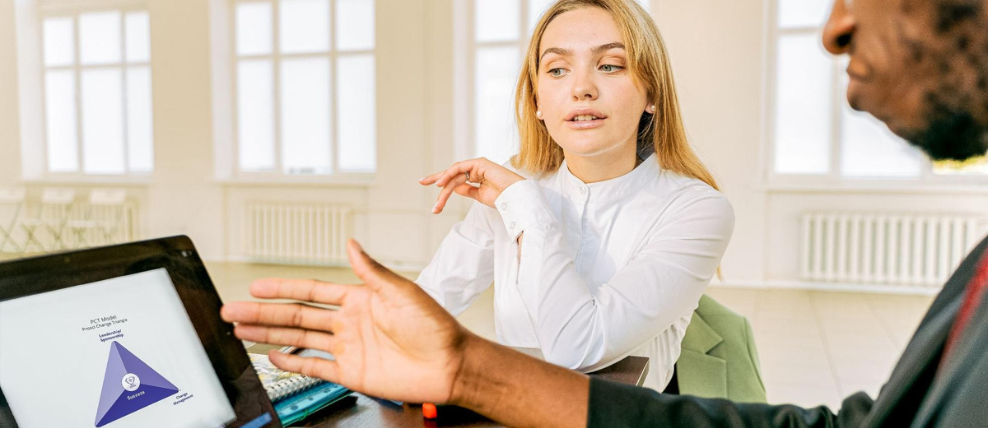
Business moves fast, and organizations must constantly change and evolve to meet new demands and generate growth. But facilitating that change isn’t always easy—it often means rethinking operational methods that employees have tried and tested over many years. Having a structured method designed to review complex processes and find areas for improvement is an empowering step toward creating meaningful change.
Process improvement methodologies allow organizations to identify inefficiencies or gaps so they can make adjustments to streamline operations.
Read on to learn about some of the most common process improvement methodologies, their benefits, and examples of real-life applications.
What Is a Process Improvement Methodology?
Process improvement involves identifying, analyzing and optimizing business processes. Organizations use process improvements to systematically evaluate workflows and operations to find process bottlenecks, redundant tasks or inefficiencies. From there, they can make changes to achieve better results.
Instead of creating your own approach, you can follow an established process improvement methodology, which offers a structured, systematic and tested framework and approach.
The results you achieve might differ depending on your unique organization. But to give you an idea, we'll walk you through some of the common benefits you can expect from process improvement methodologies.
Why Should You Use Process Improvement Techniques?
Process improvement methodologies often build in actionable tactics and techniques to support your work. They're designed to help you improve your organizational operations—but the improvements you can expect take different forms.
The top reasons organizations use process improvement techniques include:
- Achieving better efficiency – Process improvement methodologies streamline workflows and optimize resources when used successfully. That means impacted individuals can achieve more, which enables organizations to create change faster.
- Lowering operational costs – By reducing inefficiencies and increasing employee productivity, your organization can achieve more with less—making your business more cost-effective.
- Generating employee engagement – Surveys show that nearly a fifth of workers have been discouraged by a lack of role clarity and a disconnect with their company’s mission. By optimizing processes, organizations can erase that disconnect, reduce frustration levels, and boost employee morale.
It makes perfect sense then for an organization to pursue process improvements. The question is: How do you go about doing it? There are several methodologies available for this. Let’s take a look at the most common ones.
What are the Different Types of Process Improvement Methodologies?
You can approach process improvements through a variety of methodologies, each designed to deliver meaningful results. It’s important to choose one that fits your organization’s goals and workforce needs. Let’s explore six of the most common methodologies.
1. Lean
The Lean methodology is a process improvement approach (including many techniques) that focuses on minimizing waste while maximizing value. Many organizations refer to the Lean approach as the “Lean Manufacturing” methodology, but it ultimately transcends the manufacturing sector.
The reference is a historical nod to Japanese carmaker Toyota, which famously pioneered the Lean Manufacturing methodology as part of its Toyota Production System (TPS).
But it doesn’t matter whether you’re a manufacturing company looking to speed up the assembly line or a financial lender that needs to change administrative processes to meet new regulatory guidelines.
Either way, the common goal of the Lean methodology is to create more value with fewer resources by improving efficiency, reducing costs and enhancing quality.
The Lean process improvement methodology is built around five simple steps:
- Identify value – Start by determining the value each process delivers. This enables you to focus on what makes your current processes worthwhile and eliminate wasteful ones.
- Value stream mapping – Next, map out the entire process or workflow so you can visualize every step. This provides a clear view of the process in its current state.
- Create flow – Identify barriers that disrupt a workflow and then create a new workflow that minimizes those barriers to achieve the desired outcome with less friction.
- Establish pull – Lean is designed using a “pull system” driven by actual demand. After setting up a new workflow, use that new flow to complete your deliverables—without overproducing or wasting anyone’s time or resources.
- Continuous improvement – The Lean approach isn’t a one-off method. Impacted individuals should constantly be working to identify value, carry out process mapping, and establish better workflows.
This methodology can help your organization create change in an agile way that minimizes waste, keeps costs down, and delivers high value.
2. Six Sigma
Six Sigma is a data-driven methodology. Its primary aim is to improve business processes by identifying and eliminating all process defects or inefficiencies.
Organizations adopt the Six Sigma methodology because it focuses on customer satisfaction and continuous process improvement—not just one-time fixes.
There are five phases in the Six Sigma method: Define, Measure, Analyze, Improve and Control (DCAIM). Here’s how they work:
- Define – First, identify opportunities for improvement, define your project goals, and develop a project plan.
- Measure – Next, identify key performance indicators to understand process performance, collect data, and validate your measurement system to ensure data accuracy.
- Analyze – After collecting your data, examine it to identify the root cause of the problem.
- Improve – From there, it’s time to develop and implement solutions to address the root cause of the problem. Test changes through pilot schemes and optimize those processes.
- Control – The final step is to ensure your improvements are sustainable. Create control plans, monitoring systems, and a chain of responsibility to oversee new operating procedures.
It’s worth looking at General Electric (GE) for lessons on best practices for this data-driven approach.
In the mid-1990s, CEO Jack Welch famously implemented Six Sigma at GE to enhance quality and operational efficiencies. This process improvement initiative led to significant cost savings and adaptations across the company. It resulted in reduced product defects and created better customer experiences.
By championing process improvement projects to reduce unnecessary steps, teams using Six Sigma benefit from reduced variability and the ability to scale up operations more sustainably.
3. Total Quality Management
Total Quality Management (TQM) is a comprehensive, organization-wide methodology for improving the quality of processes. Its goal is to create an organizational culture of continuous improvement using a holistic approach that creates and sustains change across an entire enterprise—not just one team or department.
The core features of TQM include:
- Collaboration – TQM involves training, empowerment and fostering a culture where every employee contributes to quality improvement. This helps all impacted employees to commit to the changes.
- Process focus – When using TQM, organizations treat every activity as an opportunity to reduce errors and eliminate waste. This ensures that all initiatives contribute to the organization’s overall goals.
- Integration – TQM works to enable all departments, functions and teams to align to support quality improvement objectives.
That’s why the Ford Motor Company deployed TQM after setting up a joint venture with paint supplier ChemFil in the 1990s. Both organizations used a TQM approach to refine painting processes from preparation to application—avoiding previous friction points and creating a decisive lift in product quality.
4. Kaizen
Kaizen is a methodology that emphasizes the continuous, incremental improvement of processes, products and services over time.
The core features of the Kaizen methodology include:
- Continuous improvement – Kaizen is the Japanese term for “continuous improvement.” Kaizen focuses on making minor, gradual improvements that accumulate to create significant process improvements.
- Standardization – Kaizen promotes standardizing best practices into a process to ensure consistent service quality and performance.
- Employee engagement – The Kaizen methodology recognizes that front-line workers are best suited to identifying process inefficiencies. As a result, this structured approach ensures all those impacted are involved in process improvements.
Toyota is a well-known example of the Kaizen methodology in action. In the mid-1990s, the company implemented Kaizen in its production facilities to streamline operations and foster a more productive culture.
For instance, management collaborated directly with assembly line teams to identify inefficiencies in the production process for the Toyota Corolla. By reorganizing tools and workspaces based on employee feedback, they reduced assembly times, minimized worker fatigue, and delivered a higher-quality automobile.
5. Plan, Do, Check, Act (PDCA)
Plan, Do, Check, Act (PDCA) is a four-step iterative methodology for process improvements. The primary aim of this approach is to create continuous improvement in business processes, product development and quality management.
To help you get started, let’s quickly walk through each step of the PDCA process:
- Plan – Start by defining the problem or area that needs improvement and identifying the root causes of inefficiency. Then, develop a detailed plan of action to address those root causes.
- Do – Next, implement your plan of action. Throughout the implementation process, ensure you’re collecting data to monitor performance.
- Check – After implementing your plan, compare the results to your primary objectives. From there, you can determine whether the process improvements are working.
- Act – If your improvement efforts were ineffective, create a new plan and repeat the PDCA cycle. If they were effective, it’s time to implement the successful improvement on a bigger scale.
NASA’s Space Shuttle Program offers a textbook example of how to execute the PDCA method effectively.
After the Columbia disaster in 2003, NASA applied PDCA to investigate the root cause of the malfunction and create a solution. They then conducted rigorous testing on the alternative. The NASA team evaluated the redesigns’ effectiveness, updated inspection protocols, and adjusted shuttle flight profiles for future missions.
This systematic approach enabled scientists to create new, improved processes that reduced the risk of similar disasters ever happening again.
6. Process mapping
Process mapping is a visual representation of the steps, activities and workflows involved in a particular process. The goal is to help teams visualize and identify process inefficiencies, bottlenecks and sources of waste.
This is the methodology Amazon chose to optimize its supply chain and slash inventory costs. By utilizing process mapping, Amazon’s teams were able to visualize and enhance supply chain operations, leading to reduced cycle times and the elimination of excess inventory.
The core features of process mapping include:
- Visualization – The main appeal of process mapping is that it creates a visual representation of existing processes and remaps them into new visualizations.
- Continuous improvement – Business process maps can evolve as workflows improve. This means organizations can constantly identify improvement opportunities.
- Identification of inefficiencies – These visualizations enable you to better spot and correct potential inefficiencies.
Your organization can use a range of different visualization types. Some of the most popular are flowcharts, swim lane diagrams, value stream maps, and SIPOC (Suppliers, Inputs, Processes, Outputs, Customers) diagrams.
How Can Change Management Boost Your Process Improvements?
Process improvement methods are the ideal way to streamline business operations and introduce positive changes within your organization. But to ensure that your organization sustains process improvements, you need to help people adopt and use them. What good is a process your people avoid or can't use?
That’s where change management comes in.
By using change management approaches like the Prosci ADKAR® Model, your organization can leverage additional benefits to foster a culture of continuous improvement, regardless of the process improvement strategies you choose.
Change management prevents resistance to change
One of the top hurdles organizations face when implementing process improvements is resistance to change. Many processes are embedded deep within company cultures, making it challenging to encourage people to change how they work.
Effective change management focuses on preventing resistance. By ensuring clear communication about the benefits of process improvements, addressing employee concerns early, and fostering commitment through engagement and training, organizations can build a sense of ownership in the new processes.
This proactive approach minimizes resistance and enhances overall adoption and success.
Change management ensures process improvements are sustainable
Using change management to guide process improvements helps employees adopt new processes with the aid of continuous support, tracking and feedback. It also aligns improvements with business goals, embedding them into core values and metrics.
For example, the Colorado Department of Transportation used a structured change management approach to improve safety and process efficiency, significantly reducing employee injuries and saving costs.
Change management guides people through the psychological impacts of change
Process changes primarily focus on operations, but organizations must also consider the impact on the people responsible for those operations. A recent survey found that 53% of employees feel overwhelmed by change, highlighting the urgent need for effective change management strategies that prioritize the human side of change.
When organizations implement process changes without adequately supporting their employees, they risk increased resistance, decreased productivity and potential turnover. By addressing the concerns of those impacted by change and fostering early engagement through clear communication and training, organizations can create a culture of resilience.
This proactive approach minimizes resistance and empowers employees to embrace new ways of working, ultimately leading to smoother transitions and better overall outcomes.
Change management transforms process improvements into opportunities for both individual and organizational growth.
It’s Time to Start Improving Your Processes
Identifying areas for improvement within an organization is no small task—it requires focus, clarity and a willingness to examine every detail. Process improvement methodologies provide a structured way to uncover inefficiencies and highlight the most pressing quality issues in operations.
Yet, recognizing what needs to change is only half the battle. The real challenge lies in translating those insights into meaningful action. By addressing all impacts of change, including the emotional and psychological aspects, the Prosci Methodology for change management helps employees feel supported, engaged, and ready to adopt new processes effectively.